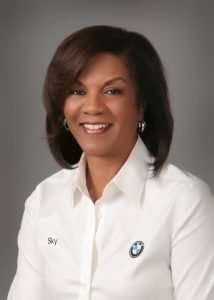
Sky Foster, Manager of Corporate Communications, BMW Manufacturing
Q: What were the primary factors that led to BMW shutting down production at the Upstate facility?
The health and protection of our associates was the primary factor that led BMW Manufacturing to stop production on Sunday, March 29. At the same time, the coronavirus pandemic had a major impact on the global supply chain and customer demand for cars.
Q: Do you all have short- and/or long-term concerns around some potential supply chain issues? If so, what actions have you all done to help offset them?
One of the greatest strengths of our plant is flexibility. Our procurement and logistics teams are very experienced in dealing with any supply chain issues, from bad weather to traffic situations. It was no different during the coronavirus pandemic, just intensified. Going forward, we will continue to be flexible and adjust our production as the supply chain dictates.
Q: You were among the employees who still were at the plant while the production line was closed. What was your primary focus during that time period?
As communications manager, my team and I had to communicate internally with our associates and externally to the media. Internally, we prepared videos, signage, a booklet and other materials to let associates know how we would protect them when they returned. Externally, we responded to media requests about our changing production operations and the global supply chain.
Q: Is BMW in conversations locally and regionally with other manufacturers regarding best practices when it comes to safety and social distancing?
Yes, BMW always seeks out best practices when it comes to the health and safety of our associates. Besides seeking the advice of the CDC and SC DHEC, we have contacts with many manufacturers and suppliers in the southeast to exchange ideas and best practices on a variety of topics.
Q: What are the most significant changes that you all have implemented to create social distancing and address health concerns?
During the non-production time, BMW implemented a variety of deep cleaning and safety measures. This included disinfecting equipment in all technologies, sanitizing workstations, remodeling layouts to enhance social distancing, and completing preventive maintenance on equipment. New guidelines and procedures have been implemented at the plant to help mitigate the spread of COVID-19. These include temperature self-checks, modified seating for cafeteria and office areas, staggered lunch schedules, and expanded cleaning practices. Face masks are required for anyone who cannot maintain the required 6-foot social distance. BMW will continue to follow these and other CDC-recommended procedures.
Q: What changes do you see in manufacturing generally and at BMW in particular due to COVID-19 that are likely to be permanent?
The most likely change we see is fewer in-person meetings and more virtual meetings.
Q: Are you all back to full production yet and if not, is there any timeline for when that should happen?
BMW’s strategy for returning to production was a phased approach. We brought back one shift on May 4 and carefully managed our supply chain over the next four weeks. On May 31, our second shift returned. Over time, as the supply chain improves, our production will continue to grow. We’re not at full production yet, but we are on our way back.
Q: What is the status at the BMW Zentrum? Is there a timeline for reopening to the public?
The Zentrum museum is tentatively scheduled to reopen mid-summer with special safety and social distancing measures in place. Tours of the manufacturing plant will be announced at a later date.