Jun 9, 2020 | Staying on Top, Uncategorized, UpstateVibe365
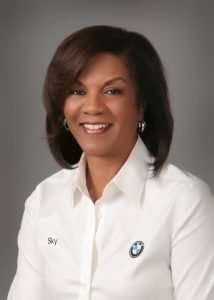
Sky Foster, Manager of Corporate Communications, BMW Manufacturing
Q: What were the primary factors that led to BMW shutting down production at the Upstate facility?
The health and protection of our associates was the primary factor that led BMW Manufacturing to stop production on Sunday, March 29. At the same time, the coronavirus pandemic had a major impact on the global supply chain and customer demand for cars.
Q: Do you all have short- and/or long-term concerns around some potential supply chain issues? If so, what actions have you all done to help offset them?
One of the greatest strengths of our plant is flexibility. Our procurement and logistics teams are very experienced in dealing with any supply chain issues, from bad weather to traffic situations. It was no different during the coronavirus pandemic, just intensified. Going forward, we will continue to be flexible and adjust our production as the supply chain dictates.
Q: You were among the employees who still were at the plant while the production line was closed. What was your primary focus during that time period?
As communications manager, my team and I had to communicate internally with our associates and externally to the media. Internally, we prepared videos, signage, a booklet and other materials to let associates know how we would protect them when they returned. Externally, we responded to media requests about our changing production operations and the global supply chain.
Q: Is BMW in conversations locally and regionally with other manufacturers regarding best practices when it comes to safety and social distancing?
Yes, BMW always seeks out best practices when it comes to the health and safety of our associates. Besides seeking the advice of the CDC and SC DHEC, we have contacts with many manufacturers and suppliers in the southeast to exchange ideas and best practices on a variety of topics.
Q: What are the most significant changes that you all have implemented to create social distancing and address health concerns?
During the non-production time, BMW implemented a variety of deep cleaning and safety measures. This included disinfecting equipment in all technologies, sanitizing workstations, remodeling layouts to enhance social distancing, and completing preventive maintenance on equipment. New guidelines and procedures have been implemented at the plant to help mitigate the spread of COVID-19. These include temperature self-checks, modified seating for cafeteria and office areas, staggered lunch schedules, and expanded cleaning practices. Face masks are required for anyone who cannot maintain the required 6-foot social distance. BMW will continue to follow these and other CDC-recommended procedures.
Q: What changes do you see in manufacturing generally and at BMW in particular due to COVID-19 that are likely to be permanent?
The most likely change we see is fewer in-person meetings and more virtual meetings.
Q: Are you all back to full production yet and if not, is there any timeline for when that should happen?
BMW’s strategy for returning to production was a phased approach. We brought back one shift on May 4 and carefully managed our supply chain over the next four weeks. On May 31, our second shift returned. Over time, as the supply chain improves, our production will continue to grow. We’re not at full production yet, but we are on our way back.
Q: What is the status at the BMW Zentrum? Is there a timeline for reopening to the public?
The Zentrum museum is tentatively scheduled to reopen mid-summer with special safety and social distancing measures in place. Tours of the manufacturing plant will be announced at a later date.
Jun 3, 2020 | Staying on Top, Uncategorized, UpstateVibe365
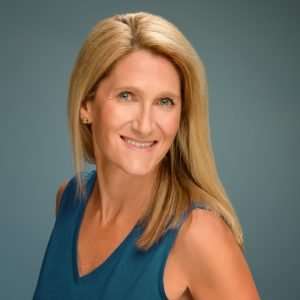
Caren Senter, Communications Manager and Program Director at Upstate International
by Caren Senter, Communications Manager and Program Director at Upstate International
Learn a new language at Upstate International this summer! Our classes have gone virtual and people are loving the new experience, according to Christine Hofbauer, Upstate International’s language school director. UI has discovered that online teaching has some definite advantages, not the least of which is ease of use and time-efficiency with no need to drive to class. Hofbauer admitted that it was a challenge to get the teachers, all of whom are volunteers, to learn the new technologies necessary to transition to online learning. Fortunately, their passion for sharing their language and culture with others was all the motivation they needed and UI has managed to not only retain its teachers but also add new ones who are teaching from their home countries of Germany and Mexico.
To everyone’s surprise, once the initial technical issues were overcome, students have found that the learning experience is enhanced in a number of ways. For example, there is more time devoted to teaching and learning as there are significantly fewer distractions and it is easier to be on time for class without worrying about traffic and weather conditions. Of course, the weather has occasionally affected internet connections, so it isn’t perfect. The classroom is also surprisingly easy for the teachers to control online, giving each student equal opportunity to practice speaking, ask questions, and engage with one another. In addition, Hofbauer noted, the teachers are better able to share materials with their students through the use of Google docs, and they have easy access to the internet during a class and can share their screen immediately with their students. Moreover, students can use the chat capabilities to ask teachers questions without interrupting the class.
Hofbauer is thrilled that UI’s students are not just from the Upstate anymore, either. While UI has broadened its horizons out of necessity, it is broadening the connections among students and teachers. Of course, Hofbauer admits that everyone misses that before- and after-class social interaction that happens in person, but they are already hearing stories of new friendships being forged online. While, initially, some students may have been a little intimidated by the online format, they became more relaxed, more comfortable, and more focused in just a few short weeks.
Upstate International has been teaching languages since its inception over 20 years ago. It began with a simple English Conversation Club that met somewhat informally to allow recent expats, and other non-English speakers, to work on their English. Hofbauer got involved with UI 16 years ago, volunteering as an English Conversation Club facilitator. Today, UI offers anywhere between 15 and 22 foreign language classes each semester.
Membership levels have remained steady in spite of the transition to online.
Most prefer the in-person experience, but there are some that we have connected with who would not have otherwise found UI. Hofbauer says that one of the most surprising benefits to the transition we have made is that we can actually offer more classes since we are not confined to UI’s 4 classrooms. Going forward, Hofbauer hopes to have more students utilize our services who are not located in the Upstate, and to increase our roster of teachers to include many more teaching from their home countries; the only challenge then will be scheduling classes that work in a variety of time zones. UI and Hofbauer are embracing the new normal and plan to continue with live online classes as an option even once some in-person classes are allowed; a combination of both will provide the greatest access to foreign language learning for our community.
You can see the full list of languages and register for UI’s summer classes here.
Jun 3, 2020 | Staying on Top, UpstateVibe365
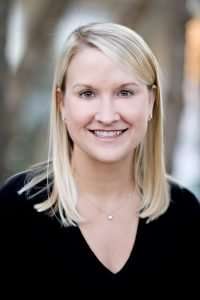
Sara Hazzard, President and CEO of the South Carolina Manufacturers Alliance
by Sara Hazzard, President & CEO of the South Carolina Manufacturers Alliance
The Palmetto State’s manufacturing sector has long been the backbone of our economy. From our manufacturing heritage rooted in textiles to the addition of other sectors including automotive, tire, aerospace, chemical and more, South Carolina’s manufacturing industry has developed a global reputation as a manufacturing powerhouse and has experienced record growth in recent years.
It goes without saying that the impact of COVID-19 on the economy has been unprecedented. Never before have our state and nation seen such an extreme economic contraction in such a short period of time. According to the South Department of Employment and Workforce (SCDEW), the South Carolina unemployment rate increased from 2.5% to 12.1% from March 2020—April 2020. Approximately 211,000 South Carolinians became unemployed during that two-month timeframe.
In April, the industries hardest hit were:
- Leisure and hospitality, down 125,300 jobs
- Professional services, down 40,700 jobs
- Education and health services, down 28,900 jobs
- Trade, transportation, and utilities, down 27,900 jobs
- Manufacturing, down 12,900 jobs
Source: SC Department of Employment and Workforce
According to an analysis by Dr. Joey Von Nessen, Research Economist with the University of South Carolina’s Darla Moore School of Business, this contraction is particularly unusual because the actions that led to it were intentional, as countries and states implemented various shelter-in-place and stay-at-home-orders, and in some cases mandatory closures. South Carolina was incredibly fortunate that from the beginning of the COVID-19 outbreak, manufacturing was considered an essential business sector and remained open for business. However, closures in other states and nations caused, and in some isolated cases continue to cause, supply chain disruptions.
Von Nessen also points to manufacturing, as compared to other sectors of South Carolina’s economy, as having a much greater impact in terms of its combined contribution to both GDP and employment. Thus, our state’s economic recovery depends on the success of the manufacturing industry.
While the overall unemployment numbers for our state, our country’s GDP growth, and many other indicators clearly show a retraction for manufacturing, it is important to note that our state and federal leaders have recognized that reopening our economy in a safe and prudent manner is a top priority. In order to jump start this effort, in April, Governor Henry McMaster established the AccelerateSC task force, which was charged with leading the state’s economic revitalization.
The task force issued its final report and recommendations last week to South Carolina Governor Henry McMaster, which include asking the General Assembly to support COVID-19 liability protection legislation and a plan for allocating the state’s COVID-19 federal funding. The federal funding recommendations include $500 million toward the state’s Unemployment Insurance Trust Fund, funding to establish a 28-day PPE state stockpile, and $80 million for broadband expansion, as well as funding for other critical needs.
Critical funding and policy decisions by the General Assembly will be essential in South Carolina’s economic recovery. Particularly, the adoption of limited COVID-19 liability protections will allow employers to operate with confidence and have certainty that if they act in good faith and implement recommended guidance to protect their employees and customers, then they will not be subject to unnecessary and burdensome lawsuits. The South Carolina Manufacturers Alliance along with a coalition of other organizations are working closely on this issue.
It is no small task, but South Carolina has a history of rising to the occasion to meet difficult challenges head-on. Some recent positive signs of our initial recovery are that, according to SCDEW, 78% of all unemployment insurance claims list a return-to-work date and continued unemployment claims numbers have begun to decline, suggesting that South Carolinians are returning to work.
In the coming months there are many unknowns that will impact South Carolina’s continued economic recovery. Will there be new spikes of COVID-19, and how severe will they be? How will the response be handled? What will the reopening of schools and childcare facilities look like, and how will this impact parents and employers? How swiftly will the consumer economy recover, and how will that impact the demand for consumer products? While the future is uncertain, TeamSC and our state’s manufacturers are focused on a safe and full recovery, and the South Carolina Manufacturers Alliance will be with them every step of the way.
ABOUT THE SCMA – The South Carolina Manufacturers Alliance is the only statewide organization dedicated exclusively to the interests of manufacturers. Its mission is to elevate the quality of life for all South Carolinians by advancing the state’s manufacturing industry. The SCMA membership is comprised of more than 200 manufacturing companies that represent more than 80,000 associates in South Carolina. For additional information about the SCMA, please visit www.myscma.com.
Jun 1, 2020 | Press releases, Regional Summit, Staying on Top
One-day Summit featuring Best-Selling Author, Richard Florida, will Move to May 2021
Greenville, SC | June 2, 2020 – Due to ongoing concerns surrounding COVID-19, Ten at the Top’s Upstate Summit originally scheduled for Wednesday, September 23rd, 2020, has been postponed to Wednesday, May 5th, 2021. The health and safety of the community has always been of the utmost importance to Ten at the Top and it is critical to play a responsible role that reflects the organization’s mission to make the Upstate region stronger together. Given the large number of attendees at this biennial event, it was clear that deferring the event to a later date was the most optimal decision to make and implement moving forward.
“We are certainly living in unique and unprecedented times. Given the importance of taking precautions to further prevent the spread of this virus, moving the event date was ultimately the best decision to make for our attendees, supporters, and the Upstate region as a whole,” said Dean Hybl, Executive Director of Ten at the Top. “This date change will allow us to enhance the overall event experience and dive deeper into Richard Florida’s focus on ‘The New Urban Crisis,’ by waiting until a more appropriate time to host a large-scale event.”
The one-day summit held at the Greenville Convention Center currently plans to maintain the focus on the “The New Urban Crisis”, as best-selling author, Richard Florida, will remain the keynote speaker. Richard Florida’s book The New Urban Crisis: How Our Cities Are Increasing Inequality, Deepening Segregation and Failing the Middle Class—and What We Can Do About It, explores the recent trend of the young, educated, and affluent flooding back into living in American cities, reversing past trends of suburban flight and urban decline. The TATT Summit Committee, made up of members from the Board of Directors, will continue to monitor the ongoing impacts of COVID-19 and could implement minor changes to the program if it seems warranted.
To learn more about Ten at the Top and the Upstate Summit, please visit https://tenatthetop.org.